Polyester, or PET to be precise, is the most widely produced textile fiber in the world. Over the past 20 years, polyester has overtaken cotton fibers, which had topped the list of the most important textile fibers for many decades. Today, more than half of all textile fibers produced are made of polyester. Accordingly, polyester production has risen from 33 to 109 million tons since 1975. According to Textile Exchange, this figure is set to rise to 147 million tons by 2030. In terms of total fiber production, the share of polyester has grown particularly rapidly, while other fibers such as cotton, polyamide and wool have remained relatively constant in comparison.
This steep polyester curve not only illustrates the unprecedented success story of polyester, but also the dramatic increase in overall textile production over the past 50 years. And what was once newly produced has to be disposed of at some point, in ever faster cycles in view of current fast-fashion consumption habits. Because resources are finite and we want to say goodbye to the crude oil from which polyester is made, it made perfect sense to look for recycling solutions specifically for polyester. After all, it takes several centuries to biodegrade and is therefore slowly but surely littering our planet.
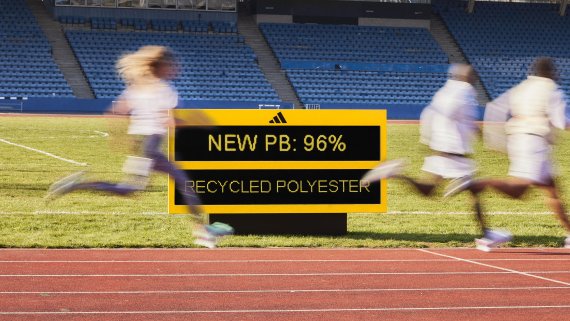
"Switching from virgin PET to rPET was relatively easy and did not pose any major difficulties for the textile industry," explains René Bethmann, material specialist and Senior Innovation Manager at Vaude, during his presentation at the Performance Days in March 2024. The production of rPET from plastic bottles has also risen sharply in recent years and accounted for 14 percent of the total polyester market in 2022. This was made possible because unmixed plastic bottles are easy to recycle without any loss of quality, in contrast to the fiber mishmash of used textiles. This is a key aspect in understanding the success of rPET made from plastic bottles.
In 1993, the US fleece specialist Polartec was the first company to use a polyester made from recycled plastic bottles instead of virgin polyester to produce fleece. Like the PET bottles themselves, the first fleece was green, 'soda bottle green' to be precise. Since then, more and more brands in the sports and outdoor industry have switched to recycled polyester or want to achieve this goal by 2030 at the latest.
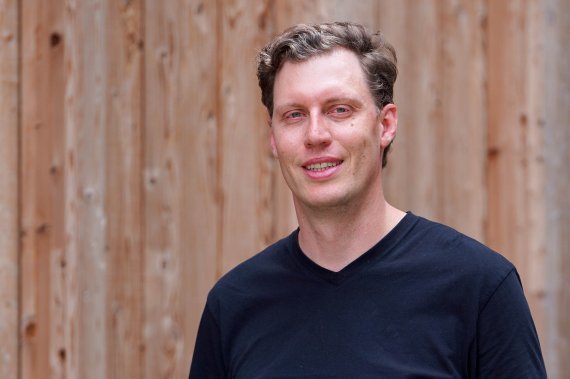
Just one percent of global rPET is currently obtained from old fibers, 99 percent comes from plastic bottles. That is far too little. This is why there are now growing concerns about this practice. Brands such as Ortovox have announced that they are phasing out the use of rPET from plastic bottles in order to replace these fibers with natural fibers or recycled fibers from genuine textile recycling. Similarly, EU legislation increasingly understands extended producer responsibility (EPR) to mean that the clothing industry recycles its own waste, i.e. that clothing production should be recycled, resources saved and waste avoided instead of solving the waste problems of the beverage industry. For example, the EU Parliament is calling for a landfill ban and fixed recycling quotas for textiles in the upcoming amendment to the Waste Framework Directive. Sustainability certificates, such as the EU Ecolabel, will also have to respond to these changes.
Textile-to-textile recycling is currently getting a boost from several sides. Firstly, from the market, "because consumers are also beginning to understand that recycled plastic bottles are not the most sustainable alternative raw material for clothing," says Bethmann. "Brands that aggressively market polyester made from plastic bottles as a sustainable solution run the risk of this increasingly being perceived as greenwashing." Manufacturers are therefore keen to find an alternative to rPET made from bottles that is at least as sustainable as possible as soon as possible.
Secondly, it must be assumed that the amount of plastic bottles available to the textile market for recycling will continue to decrease in the future. This is because the beverage industry will also be legally obliged to establish cycles and gradually increase the proportion of recyclate in bottles in the coming years. While the proportion of recyclate in beverage bottles is currently around 17%, it is set to reach 30% by 2030. This means that the textile industry is running out of recycled material. "We are cannibalizing the bottle industry," Bethmann sums it up. "There is no longer enough material available for recycling. Not in Europe, and not in Asia." What's more, bottle recycling in the beverage industry makes much more ecological sense. Bottles can be recycled almost endlessly, but if they are processed into textiles, the cycle ends there because textile-to-textile recycling is not yet available to the required extent.
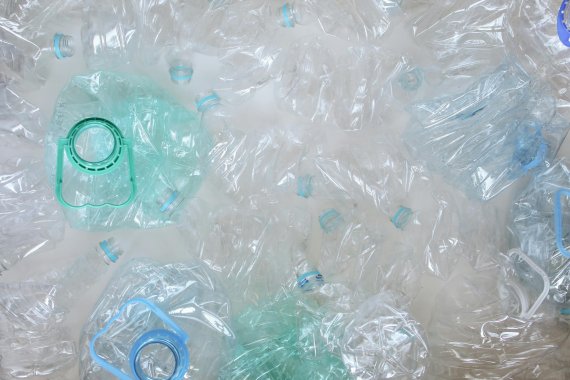
In an ideal world, we would simply switch to recycling textiles instead of plastic bottles. Unfortunately, however, this is neither quick to implement nor would it be enough. The demand for rPET from used textiles is far higher than the supply. This is mainly due to the source material, the used clothing itself. This is because used clothing is collected in many countries - in the EU, the separate collection of textiles will even be a legal requirement from 2025. But in Asia, where the majority of the synthetic fiber industry is located, the collection of used clothing is still in its infancy. This means that the old clothes have to be transported to Asia before they can be recycled, which again reduces the ecological benefit.
This is why many companies are taking the easier route and initially only recycling production waste. These are already in Asia anyway, and their use can also be ensured in large quantities. After all, recyclate manufacturers do not need a few hundred kilos of used clothing, but several thousand tons to be able to operate an industrial plant in the long term. Production waste is also easier to sort because its ingredients are better documented.
Nevertheless, despite all the hurdles, there is no alternative to textile-to-textile recycling of used clothing in the long term. The technologies are already there, not only in terms of mechanical recycling, but chemical recycling has now also outgrown the laboratory phase. Above all, there is a lack of money to establish these across the board and a lack of willingness to accept these new solutions. "All alternatives are currently generally more expensive than virgin polyester," explains Bethmann. Nevertheless, he advises against a return to virgin PET for cost reasons, not least because the CO2 tax on new polyester will also increase in the coming years and a changeover is unavoidable.
As recycling is not yet available to a sufficient extent and is unlikely to be able to meet the increasing demand for textiles alone in the future, the industry is reliant on alternatives. It therefore has high hopes for the development of polyester polymers that are not made from crude oil but from renewable raw materials such as wood or sugar cane - so-called BioPET. It is important to note that polyester is the general term for a family of materials that also includes PET (polyethylene terephthalate). Until now, when the textile industry talked about polyester, it almost always meant PET. This PET consists of 30 percent MEG (monoethylene glycol) and 60 percent PTA (purified terephthalic acid). So far, it has only been possible to biologically reconstruct MET. Just last year, the Finnish company UPM, in cooperation with Vaude, presented the first fleece with bio-based MEG. UPM sees great potential in biotechnology and is currently investing around 1.2 million euros in the construction of the world's first industrial-scale biorefinery in Leuna in Saxony-Anhalt/Germany. "The aim is to replace the remaining 60 percent," says Bethmann. "Then the CO2 footprint will be almost zero."
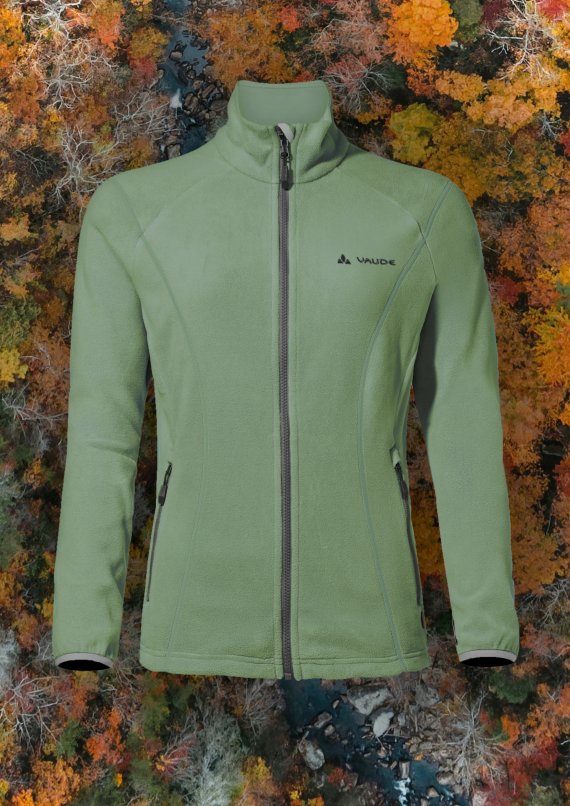
Other polyesters are also currently attracting the attention of researchers, such as PLA (polylactides, also known colloquially as polylactic acids), which are usually obtained from sugar cane, or PHA (polyhydroxyalkanoates), which are completely biodegradable under natural conditions. The latter are currently being developed by the US organization "Bottle" (stands for: Bio-Optimized Technologies to keep Thermoplastics out of Landfills and the Environment) in cooperation with The North Face to investigate their suitability as textile fibres.
The abbreviation CCU (Carbon Capture Utilization) stands for another pioneering new type of material: CCU fibres. This involves capturing carbon dioxide emissions from steelworks or petrochemical plants and converting them into ethanol through fermentation, which serves as a monomer for new polyester. If the high energy consumption during production can be covered by renewable energies, these fibers could even become climate-positive, i.e. bind more CO2 than they release.
It is uncertain which fibers will win the race in the end. "We are only dealing with around five types of material in outdoor clothing, which is comparatively few. I am therefore optimistic that we will find more sustainable alternatives," concludes Bethmann. Until the range of textile-to-textile recycled, bio-based or CCU polyester fibers has increased, he advises that product development should consider even more carefully than before which materials and properties are best suited to the desired application. In the long term, it will always come down to developing products that can be used for as long as possible before they are hopefully actually recycled at some point.
- SustainabilityBiodiversity: How the Sports Industry Can Contribute
- SustainabilityThese 5 EU rules are changing the sports industry forever
- Awards
- Mountain sports
- Bike
- Fitness
- Health
- ISPO Munich
- Running
- Brands
- Sustainability
- Olympia
- OutDoor
- Promotion
- Sports Business
- Textrends
- Triathlon
- Water sports
- Winter sports
- eSports
- SportsTech
- OutDoor by ISPO
- Heroes
- Transformation
- Sport Fashion
- Urban Culture
- Challenges of a CEO
- Trade fairs
- Sports
- Find the Balance
- Product reviews
- Newsletter Exclusive Area
- Magazine