The good news is that the outdoor industry has been a pioneer for many years when it comes to making products, manufacturing processes and supply chains more sustainable. Flagship companies such as Patagonia, Vaude, Picture Organic Clothing and many more have used their influence on the industry to inspire other companies to also take a more sustainable and better path. Ultimately, more and more consumers and retailers are demanding the same from the industry. Hardly any brand, especially in the clothing sector, has been able to ignore this trend in recent years. But we are still a long way from reaching our goal.
The necessary transformation is complex and is taking place in many areas at the same time: Whereas a few years ago it was enough to simply use more sustainable materials (for example, organic cotton, recycled polyester or other certified fibers) and, as a member of the Fair Wear Foundation, to pay attention to working conditions in the production countries, it is now clear to everyone that these measures could only be a start. The much-cited concept of sustainability encompasses far more fields of action and involves almost all stakeholders along the long path of a product's life cycle. This is now also reflected on the regulatory side, as voluntary measures have not led to the desired result.
Various European regulations, some of which have already been passed, are about to be passed or have yet to be transposed into national law, will have a huge impact on the industry. However, waiting until these laws come into force is a dangerous strategy. Achim Berg, former McKinsey & Company partner and long-standing co-author of the annual report on the state of the fashion industry, "The State of Fashion", calls for the industry to act quickly. "Waiting for regulation runs the risk of being just another excuse to disguise, delay and excuse the industry's inaction - at a time when it needs to hurry up," writes Berg. The transformation of the industry is primarily about these issues:
- Circular economy - away from the linear economic model
- Manufacturers take responsibility for the disposal of their products
- Longer service life through a right to repair
- Avoiding overproduction
- Turning away from fossil fuels
- Preventing the emission of microfibers
- More due diligence in the global supply chain
- Supply chains that do not contribute to deforestation
For a long time, companies did not need to think about how many years a product would be used, how many new resources would be needed to manufacture it and how it would be disposed of in the end. All economic activity was based on the linear "take-make-dispose" model, whose basic assumption that there are an infinite number of resources available on earth has since been proven wrong. Today, the clothing industry is also faced with the major challenge of establishing a circular model instead of the linear production and consumption model, in which resources are not "used up" as much as possible. The aim is to fully return products to the production process at the end of their life cycle in order to create new products without materials being lost or becoming waste.
Various measures are needed to achieve this: Products must be designed in such a way that they last as long as possible and still have a chance of a long life even as second-hand goods. They must be designed in such a way that they can be easily recycled, for example by using mono-materials. The more complex the material of a textile is, the more complex and therefore more expensive it is to recycle. If items are not designed to be recyclable, recycling processes are not yet economically viable.
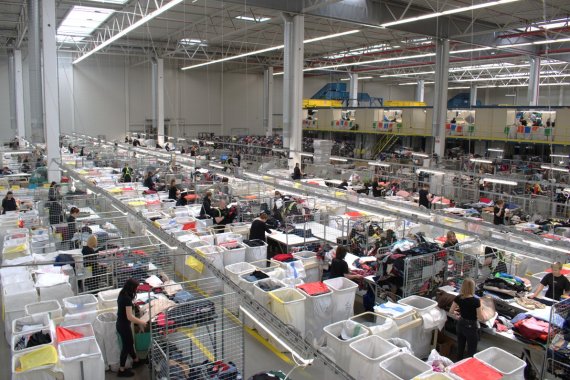
The technical capacity for high-quality sorting, collection and recycling of clothing and textiles must be created, preferably where the textiles are produced in order to avoid long transportation routes. This means that companies are called upon to establish additional relationships with recycling, collection and sorting companies beyond their usual supply chains in order to work together on solutions.
Of the approximately 7.5 million tons of textile waste generated in Europe every year, according to the European textile association Euratex, only just under one percent is currently recycled into textiles. This is set to change drastically over the next few years, partly thanks to new EU legislative initiatives. In countries such as the Netherlands, only textiles made from 50 percent recycled material are to be placed on the market from mid-2025. From 2030, the target is 75 percent. That is not far off and other EU countries will follow these measures.
Until a few years ago, it was unthinkable that companies in the clothing industry would have to think about how their product should actually be disposed of in the end. It was only NGOs such as Greenpeace that drew public attention to the major problems of textile waste, for example because synthetic fibers take centuries to decompose, because harmful substances are often released in the process and because textile waste often ends up in countries that do not have functioning disposal systems. The EU therefore wants companies to assume extended producer responsibility (EPR). This means that companies will be responsible for the disposal of their products when they are disposed of by consumers.
However, the separate collection and reuse of textiles is not yet economically viable, which is a major obstacle to the realization of a circular economy for textiles. Therefore, these systems still need to be established. This could be done either by manufacturers having to pay a mandatory levy for every product placed on the market in future, which would be invested in the development of a circular economy.
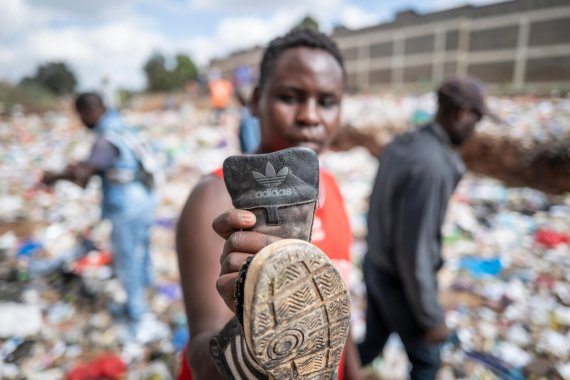
Alternatively, companies can fulfill their responsibility themselves by setting up their own collection, sorting, reuse and recycling systems, either individually or jointly. According to the Ellen MacArthur Foundation, the latter system in particular promises to be more successful, as it involves the obligated manufacturers more closely in implementing their responsibility.
So far, three EU countries have introduced an EPR policy for textiles: France, Hungary and the Netherlands. A number of other countries and regions, including Australia, Ghana, Kenya, Colombia, California, New York and all EU Member States, are currently discussing an EPR policy for textiles. The French EPR program, for example, obliges manufacturers to pay for the recycling and disposal of textile products at the end of their life. At the same time, it rewards manufacturers who bring sustainably produced items onto the market.
In order to achieve greater resource efficiency and a longer product life, it makes sense to repair defective products. With the EU's "Right to Repair" legislative proposal, companies could soon be obliged to be able to repair their products within the warranty period and beyond. Traditional companies in the outdoor industry, such as Schöffel and Lowa, have often been offering this service for a long time. Many young brands, on the other hand, which may not even have their own product development or have outsourced it completely, will have to look for partners in the future.
A new service sector is already positioning itself here and new repair centers and new, efficient software solutions are being set up all over Europe to minimize costs. For the industry, this also means ensuring the availability of spare parts and providing information on the repairability of their products.
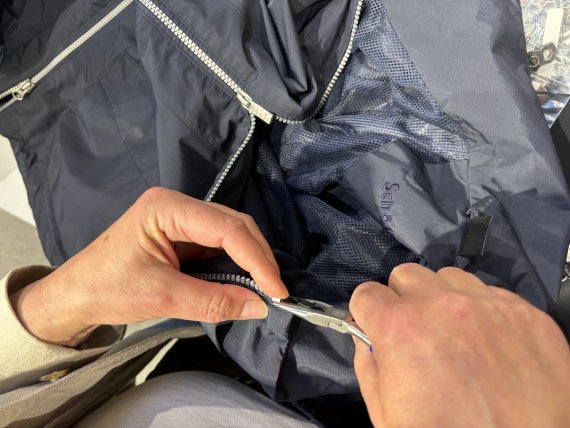
As with recycling, in the future it will also be important to set the course for good reparability at the design stage and to prioritize potential conflicts of interest. After all, functionality, design and reparability cannot always be easily combined. Companies such as Vaude have therefore developed guidelines for the repairability of their products: "Our repair index gives our customers the assurance that the repairability of Vaude products is not a coincidence, but has been taken into account in the development of each individual product," says Hilke Patzwall, CSR Manager at Vaude.
The retailers also have a duty. After all, it is from them that consumers will largely request the repair service.
There are crazy figures circulating about how much of the new clothing that comes onto the market each year is not sold at all. The figures that can be researched on the Internet range from ten to 50 percent. However, nobody knows exactly, as companies are not yet obliged to record the amount of unsold products. And they certainly do not have to disclose this data. Here, too, the legislator could soon make improvements. The EU's Ecodesign Regulation aims to establish annual transparency obligations for the disclosure of data on unsold consumer goods. This could also affect textile companies, which is actually quite likely.
Overproduction is primarily a phenomenon of "fast fashion", where large quantities of clothing come onto the market in a short space of time. What cannot be resold via remnants and third countries ultimately has to be disposed of or incinerated. But here, too, there could soon be new EU-wide regulations banning the destruction of new goods. Countries such as France have already introduced laws that prohibit the destruction of unsold clothing. There are also corresponding efforts in Germany. The devil is in the detail here: for example, it has not yet been clarified whether the recycling of new goods is also equated with their destruction.
The production of textiles from fossil raw materials such as polyester, nylon and acrylic causes large quantities of greenhouse gases. These fabrics are made from crude oil, the extraction, processing and transportation of which releases large amounts of CO2, which further contributes to climate change. Textile manufacturers around the world are therefore working on new processes to produce these important synthetic fibers in a bio-based and therefore more environmentally friendly way in the future.
This applies in particular to polyester, the most widely produced textile fiber in the world. So far, however, only one of the two components of polyester can be replaced with bio-based materials; the other component, which accounts for 70 percent, is still petroleum-based. "The aim is to replace the remaining 70 percent as well," says René Bethmann, material specialist and Senior Innovation Manager at Vaude. "Then the CO2 footprint will be almost zero." However, there are already market-ready solutions for other synthetic fibers such as nylon or polyamide. So the first step has been taken. Now the brands have to prove that they support the change in the industry and demand these new bio-based fabrics and use them in their collections - even if they are often more expensive to begin with.
Textiles are one of the main sources of microplastics. According to projections from a study by the International Union for Conservation of Nature, 35 percent of microplastics in the sea actually come from fiber abrasion from synthetic textiles. But these microfibers don't just pollute the oceans. Textile fibers that have been broken down into tiny particles can now be found everywhere in our environment: In Arctic and Antarctic ice samples, in water, in the air, in land and sea animals, in human organs and tissues. Microfibers therefore not only pollute our environment, they also damage the health of many organisms.
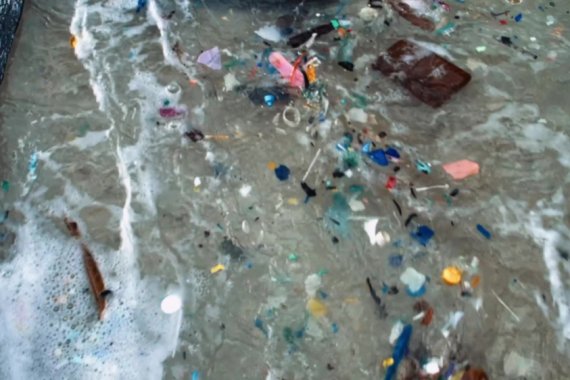
Contrary to the original assumption, this apparently also applies to natural fibers, not just synthetic, petroleum-based fibers. In terms of their environmental hazard, it does not seem to play a significant role whether these microfibers come from natural fibers or synthetic fibers. "Natural fibers also end up in the environment and remain there for a long time. This is due to the many chemical processes that natural fibers undergo, which ensure that they are not degraded either," explains Elliot Bland, researcher at The Microfiber Consortium (TMC).
The textile industry is therefore called upon to look for ways to make fibers and fabrics more robust and release fewer fragments, for example by developing new materials and fabric constructions. This includes the production phase of fibers and fabrics, including finishing, as well as the use phase by consumers and disposal. Washing machine manufacturers and wastewater treatment plant operators are also already working on new solutions. The Ellen MacArthur Foundation is therefore proposing an extension of cost recovery under the EPR to also finance the removal of micropollutants from wastewater.
In July 2024, the EU passed the European supply chain law, theCorporate Sustainability Due Diligence Directive(CSDDD), by the narrowest of margins. This obliges companies to ensure that their supply chains respect human rights and protect the environment. Due diligence makes companies responsible for all negative impacts of their business activities on the environment and human rights. This applies to all stages of production, from the raw material to the finished product. Particularly in the textile industry, which often has production in countries with problematic working conditions and low wages, companies must ensure that there is no forced labor, child labor or unsafe working conditions in their supply chains.
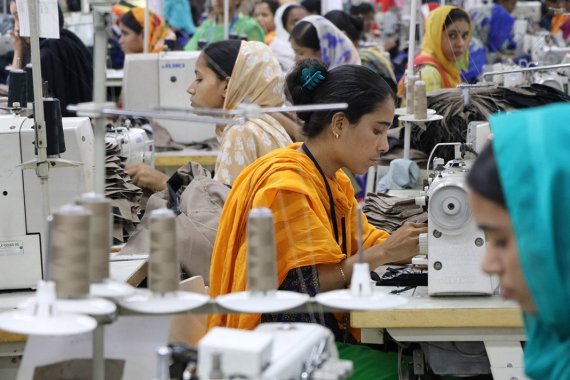
In future, companies will therefore need to know exactly what is going on in their supply chain, not only with regard to their direct suppliers, but also for subcontractors and indirect suppliers. This requires comprehensive monitoring and transparency throughout the entire supply chain. They must also carry out risk analyses and communicate these to the various stakeholders. If grievances arise, companies must take measures to improve the situation. If this does not happen, there is a risk of sanctions in the form of fines or civil proceedings such as lawsuits.
This measure was pioneered in Germany, where a German version of the law was passed in 2021.
Large brands and companies are also obliged to report regularly on their environmental performance and social responsibility for the first time.
- By 2027, companies with more than 5,000 employees and a turnover of 1.5 billion euros must comply with the CSDDD.
- By 2028, this applies to companies with more than 3,000 employees and a turnover of 900 million euros.
- From 2029, companies with more than 1,000 employees and a turnover of 450 million euros must comply with the law.
However, smaller companies may also be affected if they are part of the supply chains of larger companies that fall under the legislation.
Forests play a key role in reducing the concentration of CO2 in the Earth's atmosphere. This is because only plants have the natural ability to convert carbon dioxide from the air into solid carbon by binding it in their biomass. Forests are also important for many other aspects of nature conservation, from maintaining biodiversity to stabilizing the weather. In future, the textile industry should therefore also ensure that no forests have been cut down or damaged to produce its raw materials - such as cotton, viscose, wool or leather.
Under the EU Deforestation Regulation (EUDR), which will come into force across the EU at the end of 2024, certain raw materials and products may only be imported, exported or made available on the EU market if they are not associated with deforestation or forest degradation.
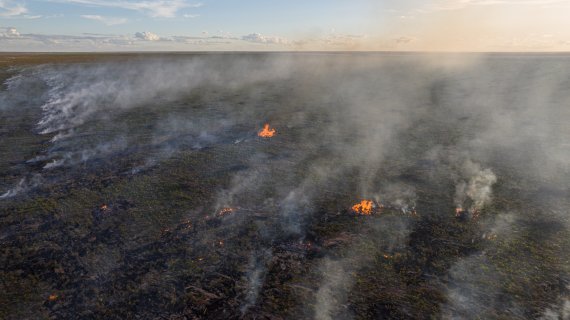
This regulation is expected to have a major impact on the global textile industry, as it requires a detailed analysis of viscose and lyocell supply chains, as well as the leather industry, whose supply chains are often opaque and global.
In recent months, reports from NGOs about illegal deforestation for the clothing industry have repeatedly reached the public. For example, the NGO Earthsight accuses companies such as H&M and Inditex of indirectly contributing to the destruction of the Cerrado region in Brazil, an area of great biodiversity. These companies are sourcing cotton from Brazilian suppliers who are involved in illegal activities in the region. "While we all know what soy and beef have done to Brazil's forests, the impact of cotton has gone largely unnoticed. Yet its cultivation has exploded in recent decades and has become an environmental disaster," says Earthsight Director Sam Lawson.
- SustainabilityBiodiversity: How the Sports Industry Can Contribute
- SustainabilityThese 5 EU rules are changing the sports industry forever
- Awards
- Mountain sports
- Bike
- Fitness
- Health
- ISPO Munich
- Running
- Brands
- Sustainability
- Olympia
- OutDoor
- Promotion
- Sports Business
- Textrends
- Triathlon
- Water sports
- Winter sports
- eSports
- SportsTech
- OutDoor by ISPO
- Heroes
- Transformation
- Sport Fashion
- Urban Culture
- Challenges of a CEO
- Trade fairs
- Sports
- Find the Balance
- Product reviews
- Newsletter Exclusive Area
- Magazine