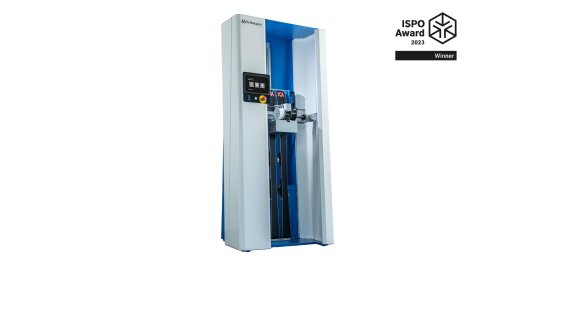
With the new Reichmann Polymat Pro, automatic base repair for skis and snowboards is more efficient and environmentally friendly than ever. It only repairs what really needs to be repaired. With this machine, Reichmann introduces a modern, precise melting process that targets damage on skis or snowboards exactly where it occurs, creating less smoke, harmful fumes, and odors in its wake. "It was important for us to develop a machine that solves the current problems in the service workshop when dealing with base repairs", explains Frederik Klingenstein, Sales Manager International at Reichmann. "There were quite a few of these, such as high energy and material consumption, strong odours, poor durability of the material and a large amount of time required. With our new technology, we have succeeded in solving all these problems at once. We are thus making an important contribution to even greater efficiency, sustainability and service quality in the ski workshop."
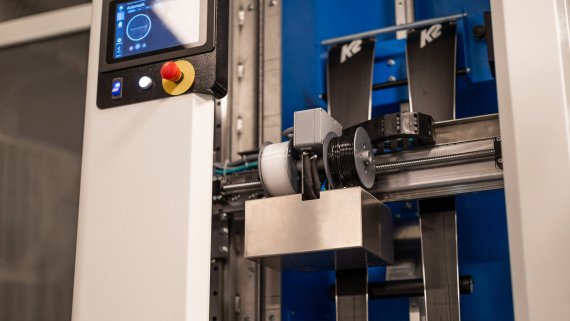
Testing has shown that this pinpoint repair method also significantly improves the durability of the repair material. You don’t impair the riding characteristics or the wax absorption of the base. As the entire base surface isn’t covered with base material during melting, no time-consuming regrinding of the ski or snowboard is necessary. This saves you a lot of time and material during the subsequent belt or stone grinding and makes the tuning process quicker overall.
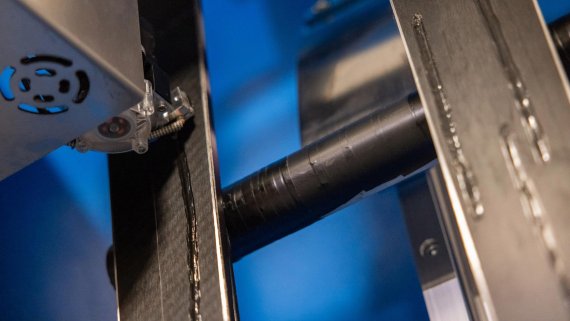
Still, the new method ensures exceptionally high-quality and even results. With the help of state-of-the-art camera technology, scratches or damage in the base can be precisely detected and locally filled. The implemented camera works with a laser, that exactly recognizes the depth, width, and height of holes and scratches in the ski or board base. This way, the machine can directly fill them with repair material and there is no need to cover the whole base. This means lower material and energy consumption, time savings, and hardly any harmful fumes in the service workshop.
The upright machine design reduces the footprint of the machine. This way, it fits also into small service workshops with reduced floor space. An intuitive user interface allows you to control the repair process effortlessly. In case you need support, the software also offers remote maintenance access. Overall, the ISPO Award jury really saw the benefit in this new technology.
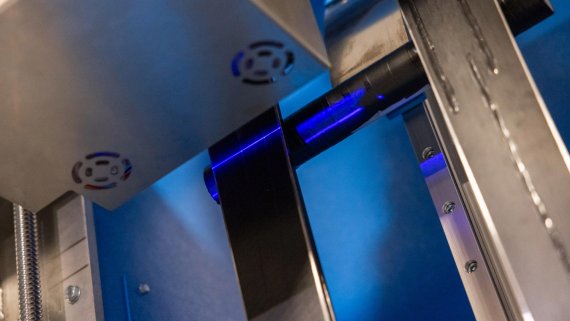
But not only the ISPO Award jury made up from industry experts and consumers could be convinced. "We presented the new machine to trade visitors for the first time at in-house events in October. We are delighted that so many visitors from different regions and countries traveled to Weißenhorn for our premiere«, says Stefan Reichmann, Managing Director of Reichmann & Sohn GmbH. He goes on to describe the added value of the new product: »In our eyes, this confirms that there is a high demand on the market for innovative solutions for professional ski servicing.«
But not only from a quality perspective but also from an employer one in retail or rental shops, the new machine can be very interesting. Stefan Reichmann explains the benefits of the Polymat Pro: »An important issue for our customers is employee retention. The harmful fumes, time-consuming work and often poor durability of the repair material currently make base repair a very unpopular task in the service workshop. With the POLYMAT PRO, base repair becomes an automated process that takes the strain off staff and generates hardly any fumes,«
- Only repairs where there is a scratch
- Requires little space due to the upright position
- Saves material & energy
- Produces hardly any smoke & vapors
- Generates no additional grinding & edge work
Product specs:
- Dimensions (W x D x H): 1050 x 785 x 2300 mm
- Weight: 380 kg
- Supply voltage: 230 V, 1PH/N/PE, 50 Hz
- Connected load in kW: 0.3
- Operating temperature: 300 °C
- Heating power: 50 W per extruder
- Release date: Winter season 2024/25
- PromotionISPO Award Winner 2025: Mythic -6 by Rab
- Awards
- Mountain sports
- Bike
- Fitness
- Health
- ISPO Munich
- Running
- Brands
- Sustainability
- Olympia
- OutDoor
- Promotion
- Sports Business
- Textrends
- Triathlon
- Water sports
- Winter sports
- eSports
- SportsTech
- OutDoor by ISPO
- Heroes
- Transformation
- Sport Fashion
- Urban Culture
- Challenges of a CEO
- Trade fairs
- Sports
- Find the Balance
- Product reviews
- Newsletter Exclusive Area
- Magazine