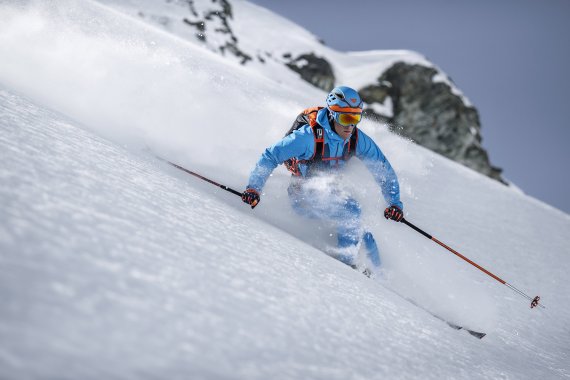
The effort in ski touring lies in the ascent: the less weight, the easier it is uphill. This applies to the entire equipment, but of course also to the touring binding: While ski touring bindings with frames require you to lift up the entire binding system, including the heavy heel piece, with every step, pin bindings simply leave out the frame's connecting bar - with significant weight savings. With this invention, Dynafit engineer Fritz Barthel laid the foundation for the worldwide success story of the pin binding in the 1980s.
But what is important today for the world market leader Dynafit when it comes to ski touring bindings? Greta Stehling, Dynafit product manager bindings, Manuel Aumann, Technical Manager Bindings and Benedikt Böhm, International Managing Director, explain it to us.
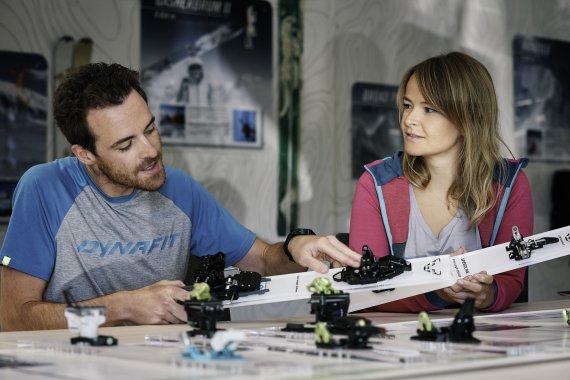
ISPO.com: Let's start with the basics - what's the difference between a pin binding and a frame binding?
Manuel: The difference concerns the fixation of the boot in the binding. With a frame model, this works - analogous to an alpine system - via a toe holder in the front and heel holder in the back, which are firmly and permanently connected to each other via a frame. With a pin binding, the whole thing happens via a metal insert specially inserted into the boot at the toe of the boot and two metal pins at the heel, which ensure power transmission.
Greta: In short, you only wear your shoe. The pin system is the much more efficient and lighter system.
Dynafit, as the pioneer of the pin binding, has over 35 years of expertise in its development. On the surface, the pin binding's high technical complexity is not apparent. Athletes use them for eight-thousand-meter ascents or descents through frozen ice walls. What makes a binding special for you?
Manuel: That's exactly what makes our bindings so special. Namely, you can't tell by looking at the Dynafit Pin binding what it does. The recesses on the toe and heel of the touring boot don't look spectacular, but they are the linchpin of the pin system. Compared to old frame bindings, we manage to implement the same safety, comfort and functions as a frame binding without the customer realizing it. The result is an absolutely technical, minimalist concept that nevertheless ensures maximum safety and is in no way inferior to a system that is ten times heavier.
Can any ski tourer, regardless of weight, skiing ability, alignment of the material "drive" a pin binding?
Greta: Generally yes. There is the right pin binding for every skier's ability and every requirement. The ski tourer must ask himself what is important to him. Weight, entry comfort, user comfort, Z-value and TÜV certification are important factors.
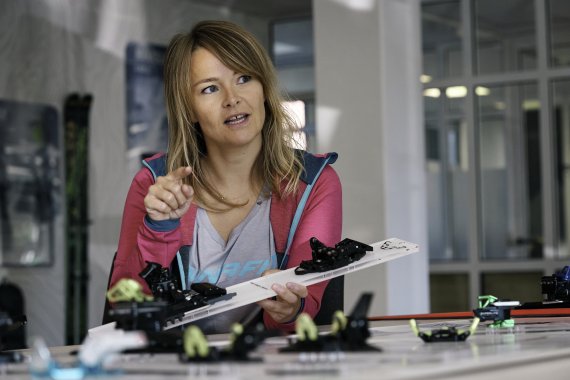
That means a touring skier is just as safe on the mountain with a frameless binding as with a frame binding?
Manuel: Correct. Our ST Rotation, for example, in combination with our certified inserts, meets the same requirements as a frame binding. The tests that are done to achieve certification are exactly the same as for an alpine ski binding. The impact tests, theöand icing tests are identical.
Dynafit offers a lifetime warranty on all bindings since November 2019. Why?
Greta: For years we have been looking at how we can design bindings to last longer. What parts need to be available and what materials need to be interchangeable in order to make this previously "internalinternal" requirement. Now we are ready to make this promise officially to dealers and end consumers.
The ST Rotation model is TÜV certified. Why are you currently the only brand that offers a current model with güTÜV certification in the program.äs?
Manuel: We wanted to undergo an independent quality control. With the TÜV test, we have an external body determine whether our own product requirements are also met. In addition, we give safety-conscious customers confirmation from an independent testing body that a pin binding passes the same tests as a frame binding.
In addition to production in Germany, the bindings are assembled by hand in your partner company, the Caritas workshops, and individually tested before delivery. Why did you decide on this elaborate process?
Greta: For reasons of quality and sustainability. We work with about 40 suppliers, over 80 percent are located in Germany and Austria. Our medium-term goal is for all suppliers to be located close to our headquarters and production facilities.
Benedikt: The close and sustainable bond production in Germany with our partner, the Caritas sheltered workshops, is immensely important to us. The partnership has strengthened over 10 years and has shown that it works. We assume social responsibility with this cooperation. We see our shoe production in Italy in exactly the same way - in other countries, we can't do that.öWe could produce cheaper in other countries, but we take the step for sustainability, quality and longevity.
The current collection from Dynafit consists of 14 models in different categories from which ski tourers can choose - depending on what is important to them. The world market leader has ski touring bindings for every application, such as the Dynafit Superlite 150 for ambitious intermediates.
- Awards
- Mountain sports
- Bike
- Fitness
- Health
- ISPO Munich
- Running
- Brands
- Sustainability
- Olympia
- OutDoor
- Promotion
- Sports Business
- Textrends
- Triathlon
- Water sports
- Winter sports
- eSports
- SportsTech
- OutDoor by ISPO
- Heroes
- Transformation
- Sport Fashion
- Urban Culture
- Challenges of a CEO
- Trade fairs
- Sports
- Find the Balance
- Product reviews
- Newsletter Exclusive Area
- Magazine