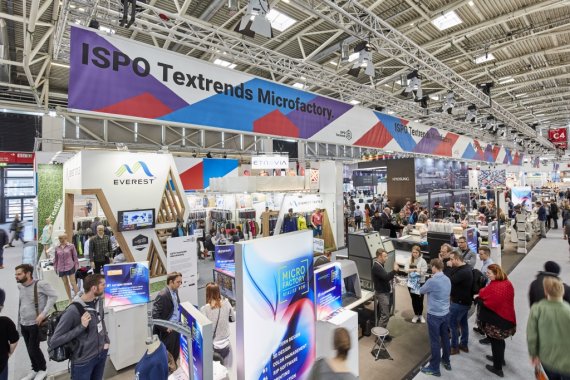
Simulate, print & cut: The future of textile printing could be as simple as that. For this purpose, the 3D simulation of clothing is directly linked to production. The DITF Denkendorf worked together with the companies Assyst, Caddon, Dürkopp Adler, Ergosoft, Mimaki, Mitwill Textiles, Multiplot, Pfaff Industrial, Stoll, Zünd and the Albstadt-Sigmaringen University of Applied Sciences to realize their vision.
From the first virtual design through digital textile printing to automated cutting and sewing, this vision could be seen at ISPO Textrends Microfactory at ISPO Munich 2019. In just 60 minutes, an individualized pair of ski pants was created in the demonstration facility. ISPO.com took a closer look at the production together with Prof. Christian Kaiser from the Albstadt-Sigmaringen University of Applied Sciences.
Professor Kaiser, the Microfactory at ISPO Munich showed a process in 11 steps, starting with the design. Why does it happen in 3D?
Christian Kaiser: Flexible production chains will no longer function without 3D in the future. Man is 3D, his clothes are 3D. So you have to build a digital twin where you can do Virtual Fit and Virtual Sampling - just on the screen.
Isn't that possible so far?
A big problem is color management - one of the biggest pains in the clothing industry. Colors on products should look like the designer had in mind. But they often don't, at least not at the beginning. One often gives away week after week with failure after failure. Aircraft fly back and forth between production and other locations - let's say the Far East and Germany. Kerosene is burned, resources are wasted - and not too scarcely.
Sounds like companies could save a lot of money.
A large brand has several thousand elements per collection. Let's assume conservatively, each element needs three iterations, then you send several thousand samples per collection across the globe. With two or three collections per year, this adds up to tens of thousands of elements. And many of these end up in the trash! This is no longer up to date and has nothing to do with sustainable production. The approval should be digital, for example virtual prototyping with simulation-supported fit evaluation and perfect color management is required.
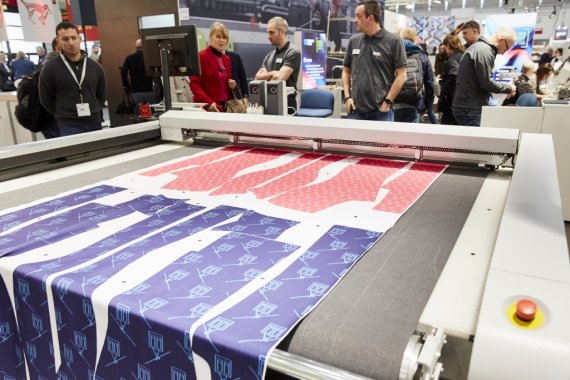
What's the difficulty here?
You can set up a printer and then it prints something - easy. The only question is whether the ink used is color-consistent, too much or too little, or whether textile specifics such as shrinkage can be taken into account. Ideally, exactly as much ink is applied as is required for a brilliant result. RIP technology, i.e. the software that controls the digital textile printer, is therefore an important process component from both an economic and ecological point of view.
Now we have a file. What's next?
This file is sent to the printer. Due to the high process stability, we use pigment printing and, in particular, sublimation printing for measuring and teaching purposes. Especially in the sports industry a lot of polyester is used, so sublimation printing is ideal. That means I print on paper, transfer the design by thermal transfer, done. A super-stable process. The only waste produced is paper and polyester - both of which are easily recyclable.
The cutting follows.
And it's fully automated. The cutter has a built-in camera and dynamically identifies the patterns. The result is a perfectly sewable piece. A prime example for industry 4.0 - and small series suitable technology.
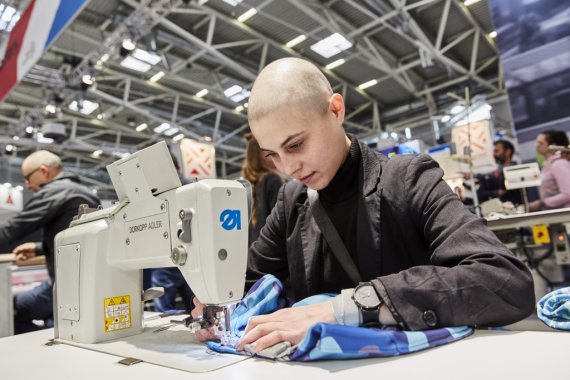
One station further, people are still working manually. There are real seamstresses sitting here.
Whether manual work or automation technology is the right choice depends on the quantity. If I cut out 12,000,000 jeans a year, I'll probably use the Kuka robot. For small quantities, however, it is usually more effective to automate digital data storage. So I have to make sure that my sewing machines are programmable and digitally adjustable. I also had to provide visualization displays for the sewing staff. For small production lines that change cyclically, this is often more effective than full automation. Because what do we humans do best? Work flexibly.
So the process remains a bit analogous.
But this is still a fully digital data model. You can see when and where which trousers were made by which seamstress. We also mix classic sewing techniques and innovative methods. Ultrasonic welding, for example, for highly flexible but bomb-proof seams. Or the tapemachine: reflective elements in clothing are an important topic in the sporting goods industry - think of passive safety. Old techniques such as thermofixing presses have disadvantages in process handling or change the colors.
Which brings us back to color management and a lot of airplanes flying back and forth.
Exactly. We're producing scrap again. Pfaff has developed a process here: you tape the elements and only where there is tape, the temperature input is done. Apparently, the process is also significantly faster. This means that this technology could also be used in Europe.
Update: Joachim Rees, a specialist for digital textile printing, grabbed a pair of the pants printed at ISPO Munich 2019 and tested them: "I wore the pants made at ISPO Microfactory for a week in the Alps at 3000m. Everything was right: Function, production, fabric & print were wonderful - the trousers were really cool. In addition, I had skis, poles, helmet, glasses and scarf adapted to the design and had a lot of attention through the design concept."
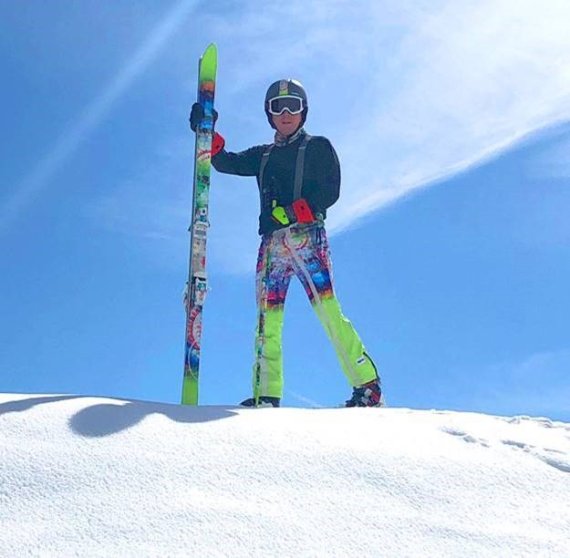
- ISPO TextrendsMore diversity outdoors: Polartec leads the way
- Awards
- Mountain sports
- Bike
- Fitness
- Health
- ISPO Munich
- Running
- Brands
- Sustainability
- Olympia
- OutDoor
- Promotion
- Sports Business
- Textrends
- Triathlon
- Water sports
- Winter sports
- eSports
- SportsTech
- OutDoor by ISPO
- Heroes
- Transformation
- Sport Fashion
- Urban Culture
- Challenges of a CEO
- Trade fairs
- Sports
- Find the Balance
- Product reviews
- Newsletter Exclusive Area
- Magazine