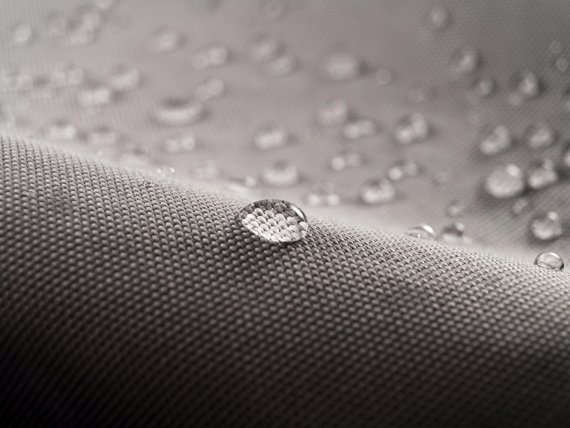
The story of Gore-Tex begins with the Teflon pan. The invention by his employer DuPont to coat pots and pans with the plastic, which had been discovered long before, gave U.S. chemist Bill Gore an idea in the mid-1950s: He wanted to use the heat-resistant material to also develop insulation for electrical cables, which were needed at the time in the fledgling computer industry, among other things. Gore found this idea so viable that he quit his job and set up his own business in 1958 with his wife Vieve in the basement of their home in Newark, Delaware.
How Gore-Tex was invented
Son Robert, one of the five children, was studying chemistry at the time and continued to experiment with the plastic. He heats the PTFE (polytetrafluoroethylene) and pulls it apart more and more. The result is a lattice that is so fine that no drop of water can fit through it. Vapor, however, can escape. The basis for Gore-Tex is invented. However, it will be some time before the membrane is used in textiles.
Groundbreaking invention as a by-product
As planned, the Gore company initially concentrates on cable insulation. Once again, it is son Robert, known as "Bob," who finds the groundbreaking way to insulate electrical cables with artificial polymer tapes during his second year of studies. Dad and Mom develop insulating wires from this in their basement workshop at home and get their first big order in 1960: 7.5 miles of cable for the city of Denver. A first factory is built. Bob files his first patent for the multi-conductor cable, and other Gore cable companies are founded.
NASA takes notice
Neil Armstrong connects his lunar module and seismographic equipment to Gore cables in 1969. Meanwhile, Bob continues his research on Earth. His expanded PTFE (ePTFE) is now being used for seals and filters. In 1972, a product called Gore-Tex hits the market for the first time, and Gore uses it to build and encase implants for surgery - artificial joints, vessels and heart valves.
Quantum leap for functional clothing
In 1976, for the first time, a textile manufacturer orders the new Gore-Tex technology from Gore for its rainwear. The membrane is bonded as a layer between the outer fabric and the lining. In 1979, Gore patents the welding seams for the multi-layer fabrics, i.e. for the laminates - at the latest, this means that there are no more obstacles to the production of all-round waterproof clothing. NASA immediately used the technology in its space suits, and numerous sportswear manufacturers from all over the world subsequently ordered the breathable membrane from Gore for their outdoor clothing.
Gore promises "Guaranteed to keep you dry".
Hundreds of outdoor textile brand manufacturers ( http://textrends.ispo.com/de/ ) have since used Gore-Tex laminates as the core technology for their waterproof, windproof and breathable products. A new standard has emerged that no one in the industry can get behind. With Sympatex, Powertex, Hyvent or Texapor from Jack Wolfskin, many competing products later entered the rapidly growing market.
Criticism of Gore-Tex
In the course of the environmental and sustainability debate, it was not long before ecological alternatives to Gore-Tex were sought and found. In order to preserve its image, W.L. Gore & Associates reacted and since the end of 2013, according to its own statement, has dispensed with problematic PFOA chemicals during production in its worldwide plants, as these can hardly be degraded in the. The company wants to make a contribution to environmental protection above all by constantly increasing the service life of its sportswear products. Most customers should be happy to hear that.
Four Gore locations in Germany
Gore has 10,000 employees worldwide in the electronics, medical, textiles and industrial products divisions. As early as 1966, a subsidiary was founded in Germany, in Putzbrunn near Munich. It is the largest of four locations nationwide with a total of about 1,500 employees. Gore has functional textiles manufactured mainly in China. In Germany, the company primarily manufactures electronic products, medical fabrics and membranes, as well as seals, ventilation technology and filters for the automotive and chemical industries.
- Awards
- Mountain sports
- Bike
- Fitness
- Health
- ISPO Munich
- Running
- Brands
- Sustainability
- Olympia
- OutDoor
- Promotion
- Sports Business
- Textrends
- Triathlon
- Water sports
- Winter sports
- eSports
- SportsTech
- OutDoor by ISPO
- Heroes
- Transformation
- Sport Fashion
- Urban Culture
- Challenges of a CEO
- Trade fairs
- Sports
- Find the Balance
- Product reviews
- Newsletter Exclusive Area
- Magazine