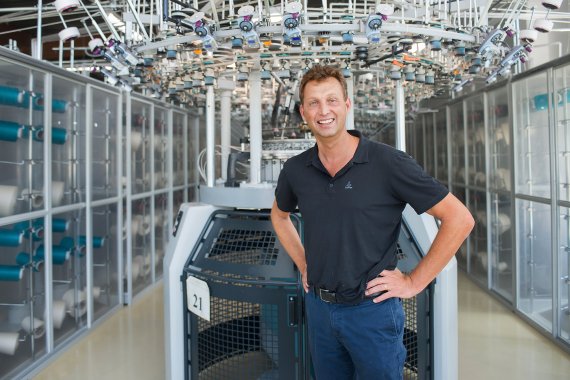
ISPO.com: Mr. Leodolter, Löffler is one of the very few companies that still produce at their company site. Why do you do that?
Otto Leodolter: Our centerpiece or gem, as we like to call it, is our knitting. We produce 70 percent of our fabric ourselves on highly specialized knitting machines that are all located here at our site in Ried im Innkreis. We don’t need production facilities in Asia. What we do need are highly specialized personnel, which is something we can find here much more easily.
How do you manage that – seeing as the majority of brands produce in the Far East to reduce costs?
By producing the majority of our fabrics ourselves, we have an essential part of our production chain in our own hands and work consciously to save many. For example, we use our resources more efficiently than others. That goes for all departments, from HR, energy and water to materials. In accordance with Austrian law, we have to pay for the disposal of all of the waste that comes from our production – we can’t just throw things away. So we are very careful to use as much of the material as possible.
And, of course, we don’t have high transport costs like others. All in all, that allows us calculations that make it possible for us to produce here. And it means that our company produces according to Austrian laws and therefore we have to and want to be conscious of environmental sustainability.
Why is it so important to you to produce in Austria?
We at Löffler are absolutely convinced that we also need to create value in Europe. Not everyone can work in the tertiary sector. It may be possible to make more money in Asia, but we also need to maintain and create workplaces in production here and ensure that we will also be able to hire qualified employees for production in the future.
Of course we aren’t the cheapest on the market, but we see that where something was produced is important to customers. Thanks to our production, we can explain why we cost more. That is an important part of our communication and an important marketing edge. That’s why we not only produce the majority of our fabrics ourselves here in Austria, we also ensure that the woven fabric and membranes we purchase were produced in Europe.
People say the sports industry has to produce faster. In order to respond to customer wishes, we need shorter lead times. Is producing yourself an advantage in that department?
We also have the problem that we have long delivery times for some materials. And if a trade fair is bumped up, we have a hard time managing the earlier timing because our production capacity is fully booked for the entire year and has to work at full capacity. Our advantage is that transportation and returns don’t need as long and we can begin producing at a later point in time.
That means when others already have to have their orders for trade fairs completed, we can still wait. That is usually convenient for retailers because they can better gauge their sales and place their orders more consciously. As a small manufacturer, we can’t work against the market trend, we have to adapt to the rhythm of the industry. I always think at some point we’re going to surpass ourselves and then skip a collection!
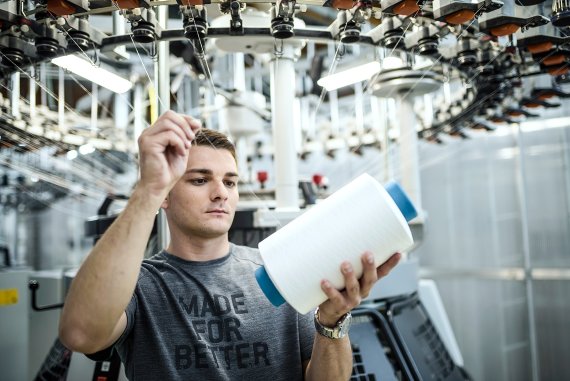
Digital processes will also be used more often for product development in the future. Do you, for example, work with 3D simulations in design yet?
We have started our first tests and definitely believe it’s the way of the future because it will help save costs and time. Not only because we will need to produce fewer samples. It’s also interesting that, for example, the 3D photos from product development can be automatically published in internal and external areas like catalogs, online shops, etc. You have to think it all through properly because the whole process has to be developed as one uniform system.
People are saying digitization will make production in general more profitable in the EU – how digitized is your production?
I see digitization on two levels: First, it’s about being able to digitize and control the individual processes, from product development to purchase decision. We are currently working hard to achieve this. Second, the aim is to increasingly be able to use robots, for example, in production. We are, of course, working with a technologically advanced machinery park, but we still need a lot of hands.
I don’t think this vision of fully-automated production will become the reality in the near future. Our small number of items alone will prevent this from happening. It’s more feasible in Asia or for heavily standardized products. One thing we do know is that people haven’t been investing in European production capacities in recent years and that also means that we hardly have any people here who are capable of working in production facilities.
That’s why you train your employees for production yourself?
That’s right. Production doesn’t just involve developers – there’s plenty of schools to train them. We also need sewers – where the proportion of women is at almost 100 percent. Those are declining professions, which is why we train people ourselves and hire all of our apprentices once they’ve completed their training. We have about 65 sewers in Austria, and another 85 in our additional facility in Bulgaria, because our capacity in Austria wasn’t sufficient. But that facility is only for sewing.
In what areas do you want to grow in the coming years?
We would like to grow father in our segments and see the largest potential for growth in cycling and outdoor sports in the years to come. Cycling is increasingly becoming an all-year sport – more and more people in cities are using cycling as a mode of transport and then becoming a recreational cyclist is the next step. Of course, the e-bike boom has contributed to this growth. Running and underwear are also developing well and we expect further growth in those areas. That means: We aren’t planning on taking on additional segments in the near future.
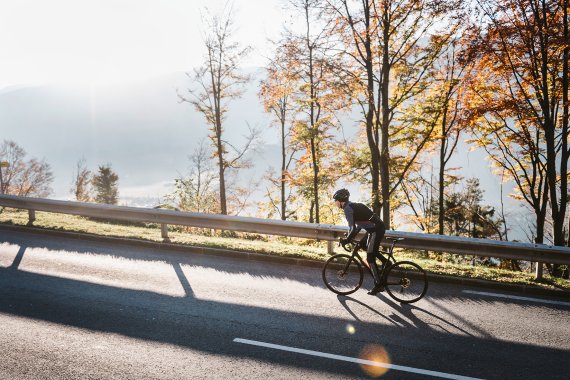
- 2017 sales: 25.03 million euros
- Number of employees: 200
- the most important markets: Bike, Nordic sports
- All markets: Bike, Nordic sports, mountain sports, running, functional underwear for endurance athletes
- the most important innovations:
transtex®: celebrating its 40th anniversary in 2018, has been constantly further developed, and is still knit at the company site in Ried im Innkreis.
hotBOND®: The hotBOND® technology is a method in which highly elastic materials are selectively welded into extremely flat seams using ultrasound.
- OutDoor by ISPOOutDoor in transition
- Awards
- Mountain sports
- Bike
- Fitness
- Health
- ISPO Munich
- Running
- Brands
- Sustainability
- Olympia
- OutDoor
- Promotion
- Sports Business
- Textrends
- Triathlon
- Water sports
- Winter sports
- eSports
- SportsTech
- OutDoor by ISPO
- Heroes
- Transformation
- Sport Fashion
- Urban Culture
- Challenges of a CEO
- Trade fairs
- Sports
- Find the Balance
- Product reviews
- Newsletter Exclusive Area
- Magazine